印刷电路板组件(Printed circuit board assemblies,PCBA)常常要经受极端气候环境条件和机械应力的考验。在电子产品组装过程中可能出现的环境变化负载包括高或低空气湿度、高或低温、低气压、迅速的天气变化、水汽凝聚、微生物影响和玷污等。所以,在保证PCBA的工作正常方面,防护和绝缘变得越来越重要,特别是要满足严格的质量和服务寿命要求的情况下。 保形涂覆是指用于保护PCBA的各种漆料体系,使之即使在不利的环境条件下也不发生失效。特别的是,保形涂覆可以避免潮湿、灰尘以及其他一些由有机溶剂及其他化学药品造成的玷污(图1)。 由于PCBA所处的工作环境中,环境条件的侵害能力和造成的负载日益严重,大多数保形涂覆相对保护能力而言可能承受了过重的负担,特别是当PCBA出现水汽凝结时。这种负担过重的现象无法归咎于涂层聚合物或者粘结剂的效用或者品质不能达到要求,而应当归咎于所用的涂层厚度。 由此可见,待保护面的边缘覆盖很重要。然而,利用标准的喷涂系统虽能改善边缘覆盖,但却会存在某些缺陷。
可供选择的保形涂覆 根据IPC标准2221,“关于印刷电路板设计的一般性标准”,保形涂覆的推荐厚度为:丙烯酸、环氧与氨基甲酯树脂30×130mm,有机硅树脂50×150mm。层厚对涂层的保护效果有极大的影响。 层厚几乎与抗渗移能力直接成正比,使层厚增加一倍几乎可以让抗渗移能力和保护作用提高一倍。问题的解决办法看上去十分简单。采用现有的保形涂覆,只需简单的增加其涂层厚度,其防护效果就得到了改善。然而,这种做法有若干不利的影响。 对大多数保形涂覆来说,漆膜的干燥速率取决于其厚度。越厚的膜,干燥得越慢,因为其溶剂从未干燥的漆膜逸出要经过的距离更长。当保护漆在氧化气氛中干燥时,为了充分固化漆膜,空气中的氧气的渗入深度必须更大。 干燥过程中必须经历的这些延迟不仅仅是线性增长的;层厚加倍并不意味着干燥时间仅仅翻番。干燥速率是呈指数形式变化的;双倍的层厚对应的干燥时间是原来的四倍。所以要实现预定的特性,如粘附性和电气绝缘性能,要花费的时间将要长得多,涂层质量对PCBA中不可避免的层厚波动也更加敏感。此外,由于有较大的溶剂残留,这些涂层也对早期包封或者环境条件变化极为敏感。 第二种方法是进行两次防护漆涂覆,这也是实践中经常采用的方法。一般来说,这种方法也要受到与上面提到的各种因素的影响。工艺时间会大大延长。由于对工艺条件的控制变差,可能会出现起皱或者拉长现象。 可供选择的第三种方法是使用固体物质含量更高的防护漆体系。然而,即使使用了较少的溶剂,这些体系所需的干燥时间仍不得不延长。如果在保证粘滞性不变的情况下提高固态物的含量,就必须使用小分子量的树脂。于是,由于要实现成膜时必须让更多的树脂分子完成交联,所以干燥循环反而变慢。此时同样存在层厚更厚而溶剂从涂层中逸出变慢的现象。 第四种方法是无溶剂涂料,它从技术和环保的角度来说将是一种可取的方法。它们的化学基本原理一般与注塑成形合剂或注塑成形树脂的相似。从这一意义上来说,注塑成形合剂、注塑成形树脂与保形涂覆之间的界限并不分明。注塑成形树脂及合剂的缺点已是众所周知。这些主要由两种组元构成的体系,其粘滞性更高,而且由于需要用到两种组元,所以工艺的成本比保形涂覆方法更高。 第五种可供选择的办法是粉末涂覆,但这些涂层的固化需要130°C以上的高温。此外,细微结构的浸润问题,和元件的下部填充都是其缺陷。 第六种方法是单组元潮湿固化的聚亚氨酯。不过,它们有如下缺点:干燥过程同样缓慢、对PCBA表面的潮气敏感、储存稳定性有限等。当容器必须打开数次时,最后一个不利因素表现得极为突出。 最后不得不提到有特色的、传统的紫外线(UV)固化漆,它们的粘度很小,而且无需溶剂,干燥过程特别快。然而,它们亦有相对明显的缺点:PCB板上,只有在紫外辐射能直接触及粘合剂的区域,所涂覆的防护漆才能干燥。在阴影区,特别是在元件下方,最初不会发生任何固化。所以,这些区域的防护漆体系保持原有的粘性,不能提供所需的保护作用,这些面积是防护力被严重削弱的区域,它们甚至可能会导致整个PCBA的失效,特别是更出现严重的环境变化的时候,如水汽凝结。 采用UV漆时,常常需要进行一次温度在100°C以上的加热后处理。这一处理会让阴影区域出现成膜现象。然而,这种后处理会大大限制某些漆的使用,甚至让某些漆无法使用。
一种新的防护漆替代产品 最近开发出了一种新型的厚膜漆,它有可能消除与PCBA的厚膜涂覆有关的无数问题。这种漆基于共聚胺基甲酸脂(PUR)和聚丙烯酸酯材料,它们采用了两种不同的化学固化机理,这两种机理能在干燥过程中补充对方的不足。新型的厚膜漆只需极短的工艺处理时间,而且能改善对天气环境变化、化学伤害及机械负载的防护作用。 第一个阶段,漆先经受UV干燥,经过很短时间后,漆就能干燥到可以随意拨弄的程度了。UV交联化进行得很快,所产生的保护性薄膜可经受力负载,而且其电气绝缘性能满足对保形涂覆的需要。 固化可以在标准的UV固化设备中完成。UV射线的良好分布可以防止元件附近出现阴影区,确保元件侧面的受到恰当的曝光和固化,对元件的防护将十分有利(图2)。 在第二阶段,即缓慢干燥阶段,由空气中的湿气引起的化学结构交联,特别的,在光致交联无法实现的UV阴影区,也会发生交联。通过这种交联机制(PUR固化),从空气中扩散到聚合物中的潮气“被截获”,形成聚合化,进一步使阴影区的防护漆固化。这一反应要缓慢得多,在约8~14天后才最终停止,具体时间与环境条件有关。 负责阴影区固化的UV官能团和异氰酸酯官能团将附着在同一聚合物分子上。这种双重功能特征保证了极高的阻挡作用和质量,因为软树脂膜里不留下任何未实现交联化的粘合剂。在一次涂覆循环中用这种防护漆所能达到的层厚范围是200mm×2000mm(图3)。 这种厚膜漆提高了阻挡能力,而且干燥过程的加工极为方便。如果膜厚合适的话,这种漆还能改善对元件固定作用,以防止振动的影响(如造成电接触脱开)。由于它采用双重交联机制,与类似的传统UV体系相比,这种漆的交联过程造成的收缩问题更小。因为它是无溶剂的,所以在实现了对PCBA更好保护的同时,也对环保有利。 这种新漆对凝聚水汽的阻挡能力亦高于传统的保形涂覆。这是因为交联度较高、涂层较厚的缘故。此外,任何在固化完成前渗入的水汽都被截获并用于进一步的交联,这样就改善了体系的性能。 这种新漆对浓酸、浓减以及其他腐蚀性介质有更好的化学耐受力。此外,它可望有很好的总体电性能和抗电痕能力。由于粘合剂有特殊的化学结构,经过复合固化过程之后,能够与常用的电子产品衬底实现良好的附着。除了交联过程中发生的收缩所引起的残余应力外(对于厚膜漆尤其如此),还必须考虑热残余应力及其影响。例如,由于涂覆厚度更高,而且可能出现部分填满的情况,厚膜漆能够比传统的、涂覆厚度较薄的保形涂覆传递更大的力。传统的保形涂覆更容易发生开裂而不是损坏PCBA。 涂层是由热膨胀系数(CTE)不同的材料构成时,如果要承受热冲击的话,热残余应力的出现将不可避免。这里,材料不同的杨式模量和CTE是主要的诱因。在这些情况下,能在室温下固化的、收缩很小的、无溶剂的合剂体系,就显得十分有利。这种类型的厚膜漆以环境空气中的水汽实现固化,过程较长,所以将UV固化不可避免引入的残余应力这一副作用释放掉。结果,能保证良好的附着性,即使对金属衬底也是如此。 由热膨胀系数不同而造成的残余应力s*可以由如下公式表出:
式中EPolymer代表杨式模量,聚合物代表聚合物涂层的热膨胀系数,衬底代表衬底的热膨胀系数;例如基底材料、焊点或元件的塑料涂层。 如果过渡状态是在玻璃化转变温度之上完成的,那么材料特性会出现显著的变化。于是,采用杨式模量和CTE在所要求的温度范围内(往往是-40℃~120℃)波动尽可能小的防护漆将是有利的。杨式模量小对避免残余应力来说,也是有利的。举例来说,新的厚膜漆提供了这种能力,因为它的组成保证了即使在更低的温度下也能保持较高的弹性(图4)。 由于其玻璃化转变态处于负温区,所以可预测出的随温度变化而变化的变形容易被松弛掉。结果就保证了张力最小,这可以从其更好的热冲击耐受力可以看出。 对于粘度更高的产品来说,必须特别注意元件的浸润和填充不足(underfilling)。这种新漆是一种表面活性系统,能够确保大型集成电路的充分下填充。图5示出厚膜漆在毛细作用影响下在元件下方流动的情况,而漆的物理流停止在元件的上面一侧。 图6示出了涂覆在IC上的厚膜漆隆起的区域,其边缘长度为25mm。PCB上的漆流动约1cm后,IC的下方被充分填满(图7)。为了展示这种影响,将IC的引线剪断并让其底面朝上放置,由此展示下填充情况。这样,就实现了元件的充分的下填充,实现了安全和充分的包封(图8)。
结语 上文讨论的一种基于共聚胺基甲酸脂(PUR)和聚丙烯酸酯材料的新型厚膜漆,在若干方面优于传统的保形涂覆。虽然涂覆厚度较大,但由于采用了同步进行的二元固化工艺,所以只需极短的处理时间。通过即使在阴影区也能进行的进一步反应,这一新型的厚膜漆能够提供快速的UV固化和交联化。这种单组元体系还能提供与双组元体系相同的耐受能力。这种厚膜漆实用的膜厚范围上限高达2000mm。它综合了耐受能力更高和干燥工艺简便易行的优点。在可以实际承受的天气环境、化学和机械负载范围内,它的效用最高。这种漆可以为PCBA提供更好的保护,而且能可以对元器件实现良好的下填充以保护其不受振动的损伤。
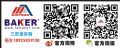 |